Советские инновации в бронетехнике
В какой-то момент пластики превратились в отличную замену классическим металлам и, тем более, дереву. Им нашлось применение даже в создании боевых машин, где они показали себя с лучшей стороны. Впрочем, самые радикальные проекты с использованием композитов остались лишь на бумаге.
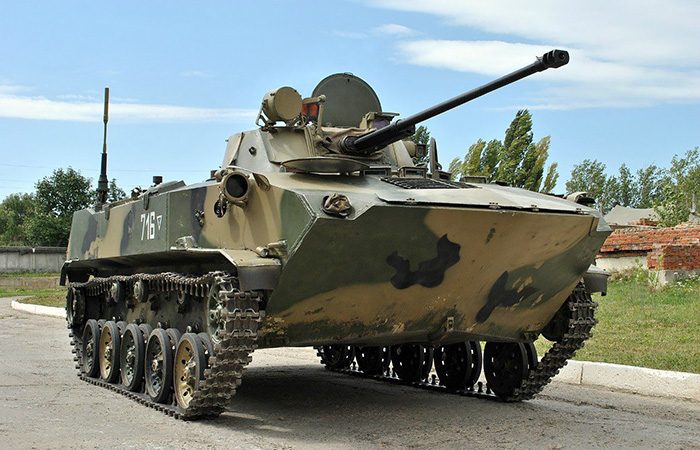
Один из таких проектов в начале 1990-х годов обсуждался на страницах известного издания, но по известным причинам всерьёз его никто не воспринял.
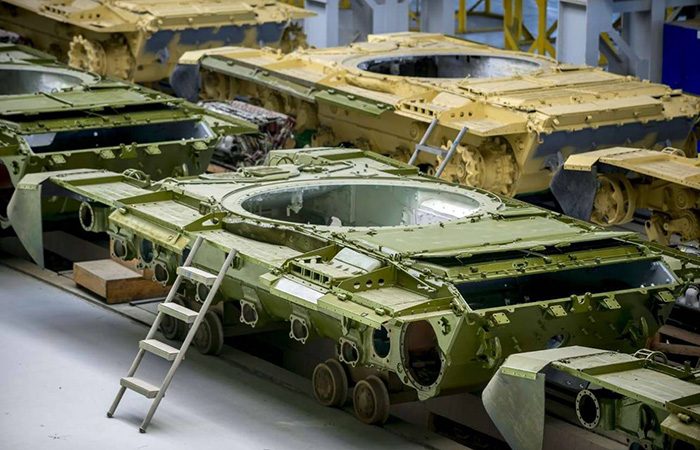
Корпуса танков.
В середине прошлого века советские конструкторы всерьез задумались о применении композитных материалов в бронетехнике. Инженеры стремились решить сразу несколько задач: снизить массу боевых машин, улучшить их баллистическую защиту и упростить производство. Одним из перспективных направлений было использование стеклопластика и керамики в конструкции корпуса боевых машин. Стандартные бронекорпуса традиционно изготавливались из стали или алюминиевых сплавов с их преимуществами и недостатками. Сталь давала надежную защиту, но имела большой вес, что снижало подвижность машин и увеличивало нагрузку на ходовую часть. Алюминий, напротив, позволял снизить массу, но уступал стали в стойкости к бронебойным боеприпасам. В поиске альтернатив инженеры обратили внимание на композиты.
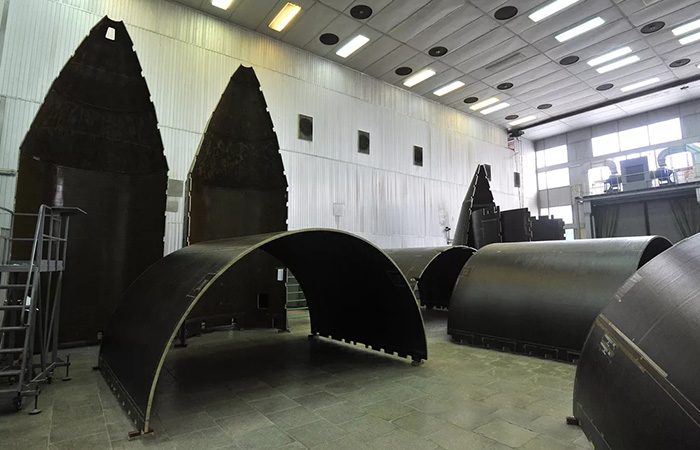
Обтекатель ракеты из композитов.
Стеклопластик, который широко использовался в авиации и судостроении, показал высокую прочность при сравнительно малом весе. Совместив его с керамическими элементами, можно было бы получить корпус, обладающий одновременно легкостью и высокой баллистической стойкостью. Предполагалось, что стеклопластик будет основным несущим материалом, а керамика станет дополнительной защитой от бронебойных боеприпасов. Это сочетание казалось перспективным, особенно для воздушно-десантной техники, где каждый килограмм играет решающую роль.
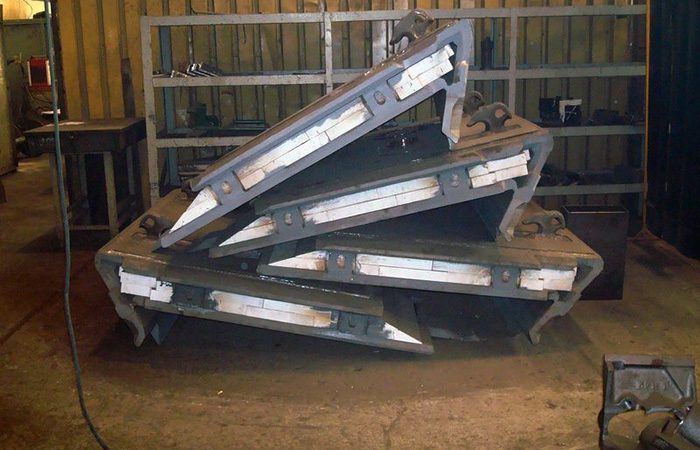
Панели брони танка.
Использование пластиков и композитов в бронетехнике сулило множество преимуществ, одним из главных было снижение массы. Легкую боевую машину легче транспортировать воздушными средствами, она может быстрее передвигаться по пересеченной местности, пересекать лёгкие мосты и иметь более высокую удельную мощность. Ещё один плюс – улучшенная баллистическая защита. В отличие от металлических бронелистов, композиты не дают осколков. Керамическая часть корпуса поглощает часть энергии, а стеклопластиковая основа предотвращает дальнейшее разрушение. Такая многослойная конструкция может существенно повысить шансы на выживание экипажа.
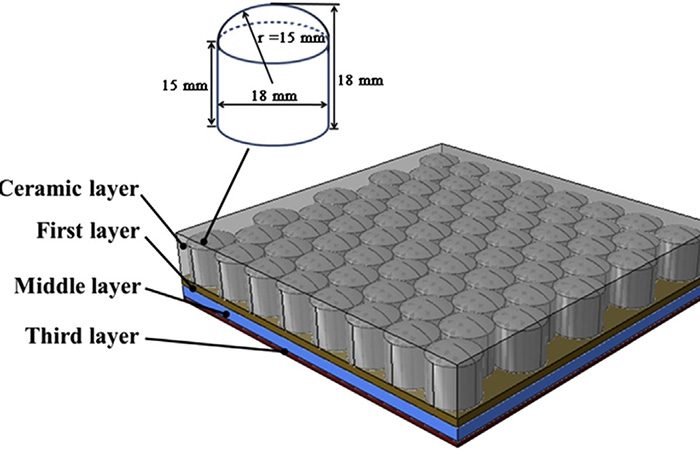
Броня с керамическим композитом.
К тому же, все металлы подвержены коррозии, особенно в условиях высокой влажности и перепадов температур, а композитные материалы лишены этого недостатка. Они не боятся воды и устойчивы к воздействию большей части химических веществ, что могло бы снизить затраты на обслуживание техники и продлить срок её эксплуатации. Кроме того, для производства техники из композитных материалов не требуются трудозатратные металлургические процессы и трудоемкая механическая обработка. Уже известные в то время технологии формования были гораздо проще, и с их помощью можно было изготовить детали сложной формы с минимальными затратами. Идея широкого использования композитов была очень перспективной и многообещающей.

Стеклоткань.
В 1990 году в одном из изданий, посвящённых бронетехнике, озвучили интересную идею – в качестве основного материала для корпуса использовать композиты на основе стекловолокна (стеклопластик), а не классическую бронесталь. В проекте предполагалось использовать панели из стеклопластика толщиной около 15 мм, усиленные керамическими пластинами толщиной примерно 8 мм. Такая комбинация должна была обеспечить защиту от бронебойных пуль калибра 7,62 мм, но при этом вся конструкция должна была весить гораздо меньше, чем полностью стальной аналог. Основным методом производства должно было стать контактное формование, широко применявшееся в судостроении.
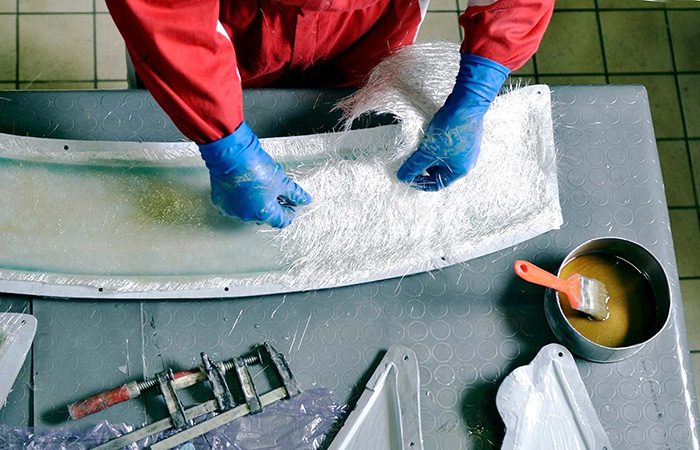
Создание детали из стекловолокна и смолы.
По сути, это было послойное укладывание стеклоткани, пропитанной полимерными смолами, а после затвердевания материала получалась прочная монолитная структура, которая могла выдерживать значительные механические нагрузки. Этот процесс позволял создавать элементы корпуса без сварки и сборки из множества деталей. Роль броневой защиты выполняли керамические элементы. Они вкладывались в специально подготовленные ячейки внутри стеклопластиковых панелей, а после повреждения их можно было бы заменить без полной разборки корпуса. Конечно, были и другие интересные нюансы, например, улучшенная термоизоляция. Впрочем, всё это не меняло того факта, что озвученные мысли плохо соотносились с реальным положением вещей.
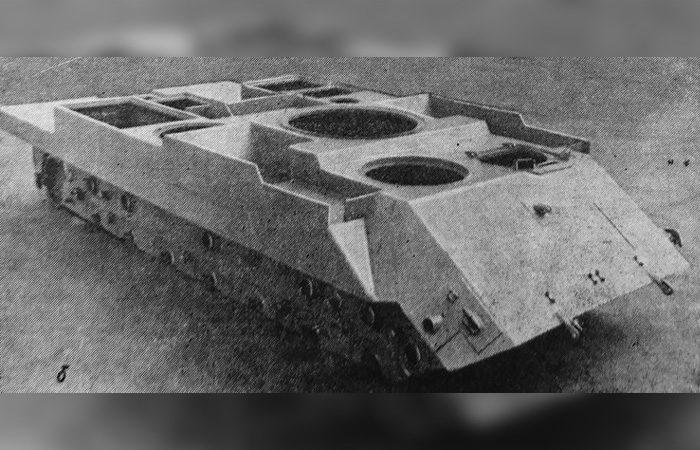
Склеенный из стеклопластика корпус.
Несмотря на очевидные преимущества композитов, у их использования для создания бронетехники имеются большие недостатки. Одна из главных проблем – сильное снижение прочности во время длительной эксплуатации. Стеклопластик, который по своей сути не является монолитным, со временем изнашивается и теряет свои свойства под воздействием ультрафиолета, механических нагрузок и перепадов температур. В боевых условиях, где техника подвергается экстремальным нагрузкам, это наверняка привело бы к быстрому износу корпуса и поломкам. Другой важный момент – сложность ремонта. Если металлическую броню можно было как-то восстановить в полевых условиях, то поврежденные композитные панели ремонту не подлежат вообще, их требуется полностью менять независимо от степени повреждения. То есть оперативный ремонт в полевых условиях превращается в большую и труднорешаемую проблему.
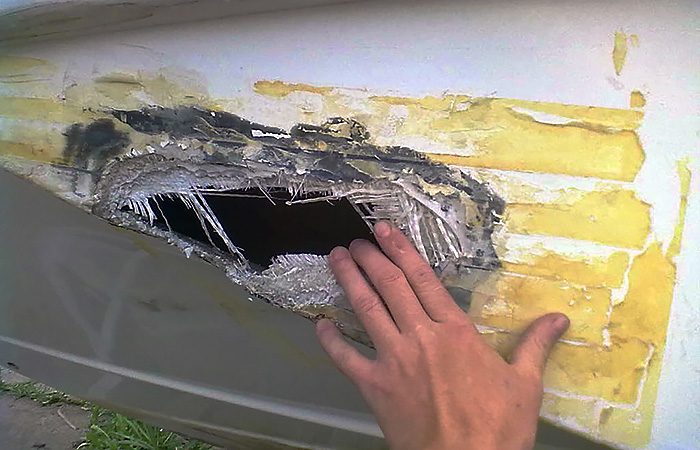
Стеклопластик приходит в негодность от повреждений.
Кроме того, керамические элементы, применяемые для усиления защиты, хоть и обладают высокой твердостью, но остаются хрупкими. При сильных ударах или многократных попаданиях их структура получает большие повреждения, а общая прочность сильно снизится. Конечно, эта проблема довольно быстро решается их полной заменой, но в полевых условиях это наверняка было бы не так просто, как кажется. Не меньше трудностей доставляет химический состав стеклопластика, а точнее, его реакция на высокую температуру. Во время нагрева композит выделяет токсичные вещества, поэтому любой пожар будет нести дополнительную угрозу для экипажа. По этим и многим другим причинам никто всерьёз и не рассматривает создание лёгкой бронетехники из подобных материалов. Уж слишком много сложностей возникает и в процессе производства, и в эксплуатации.
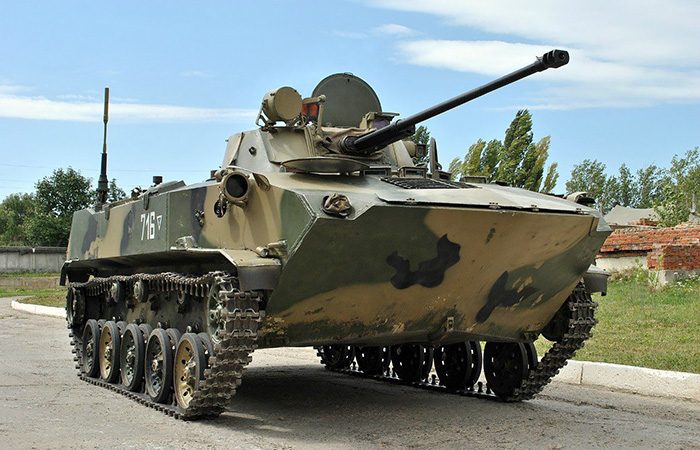
Один из таких проектов в начале 1990-х годов обсуждался на страницах известного издания, но по известным причинам всерьёз его никто не воспринял.
Концепция боевой машины из пластика
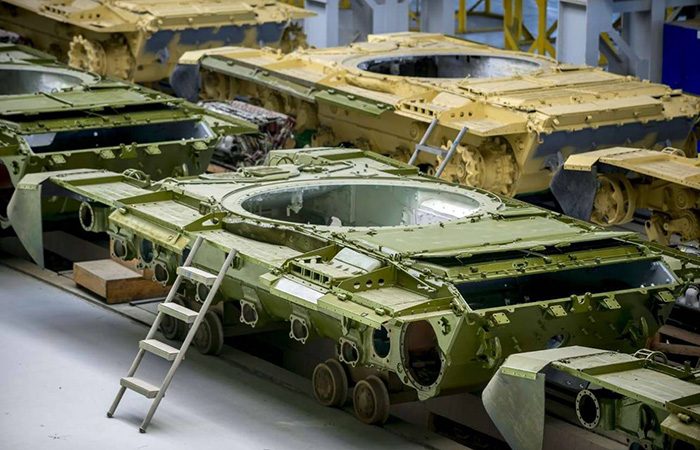
Корпуса танков.
В середине прошлого века советские конструкторы всерьез задумались о применении композитных материалов в бронетехнике. Инженеры стремились решить сразу несколько задач: снизить массу боевых машин, улучшить их баллистическую защиту и упростить производство. Одним из перспективных направлений было использование стеклопластика и керамики в конструкции корпуса боевых машин. Стандартные бронекорпуса традиционно изготавливались из стали или алюминиевых сплавов с их преимуществами и недостатками. Сталь давала надежную защиту, но имела большой вес, что снижало подвижность машин и увеличивало нагрузку на ходовую часть. Алюминий, напротив, позволял снизить массу, но уступал стали в стойкости к бронебойным боеприпасам. В поиске альтернатив инженеры обратили внимание на композиты.
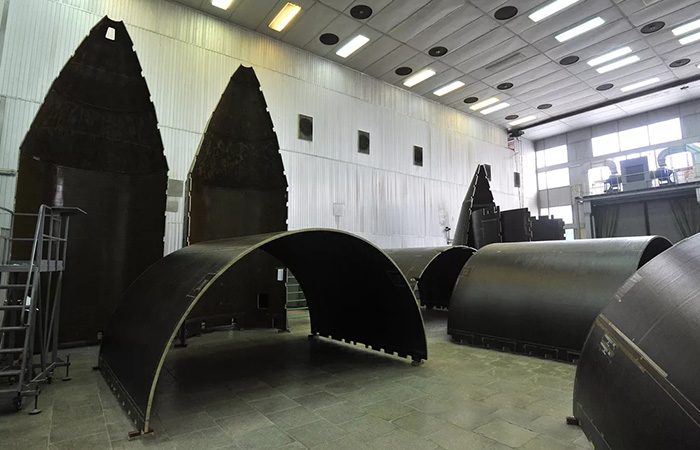
Обтекатель ракеты из композитов.
Стеклопластик, который широко использовался в авиации и судостроении, показал высокую прочность при сравнительно малом весе. Совместив его с керамическими элементами, можно было бы получить корпус, обладающий одновременно легкостью и высокой баллистической стойкостью. Предполагалось, что стеклопластик будет основным несущим материалом, а керамика станет дополнительной защитой от бронебойных боеприпасов. Это сочетание казалось перспективным, особенно для воздушно-десантной техники, где каждый килограмм играет решающую роль.
Преимущества применения пластика в бронетехнике
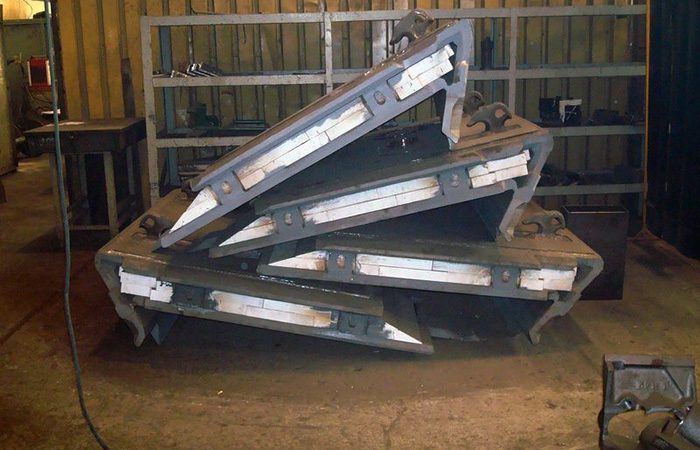
Панели брони танка.
Использование пластиков и композитов в бронетехнике сулило множество преимуществ, одним из главных было снижение массы. Легкую боевую машину легче транспортировать воздушными средствами, она может быстрее передвигаться по пересеченной местности, пересекать лёгкие мосты и иметь более высокую удельную мощность. Ещё один плюс – улучшенная баллистическая защита. В отличие от металлических бронелистов, композиты не дают осколков. Керамическая часть корпуса поглощает часть энергии, а стеклопластиковая основа предотвращает дальнейшее разрушение. Такая многослойная конструкция может существенно повысить шансы на выживание экипажа.
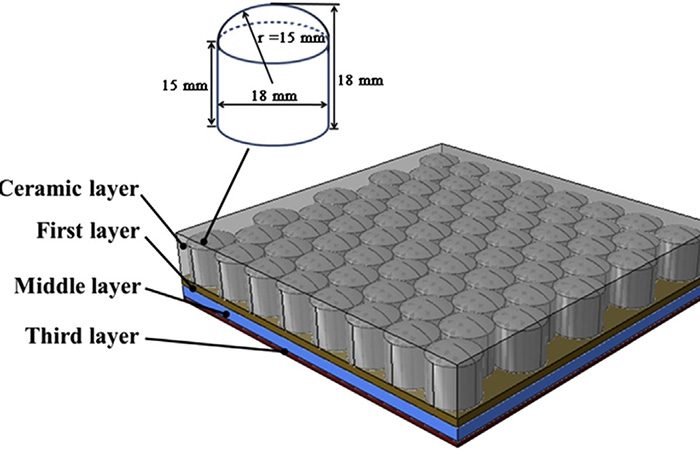
Броня с керамическим композитом.
К тому же, все металлы подвержены коррозии, особенно в условиях высокой влажности и перепадов температур, а композитные материалы лишены этого недостатка. Они не боятся воды и устойчивы к воздействию большей части химических веществ, что могло бы снизить затраты на обслуживание техники и продлить срок её эксплуатации. Кроме того, для производства техники из композитных материалов не требуются трудозатратные металлургические процессы и трудоемкая механическая обработка. Уже известные в то время технологии формования были гораздо проще, и с их помощью можно было изготовить детали сложной формы с минимальными затратами. Идея широкого использования композитов была очень перспективной и многообещающей.
Планируемые материалы и методы сборки

Стеклоткань.
В 1990 году в одном из изданий, посвящённых бронетехнике, озвучили интересную идею – в качестве основного материала для корпуса использовать композиты на основе стекловолокна (стеклопластик), а не классическую бронесталь. В проекте предполагалось использовать панели из стеклопластика толщиной около 15 мм, усиленные керамическими пластинами толщиной примерно 8 мм. Такая комбинация должна была обеспечить защиту от бронебойных пуль калибра 7,62 мм, но при этом вся конструкция должна была весить гораздо меньше, чем полностью стальной аналог. Основным методом производства должно было стать контактное формование, широко применявшееся в судостроении.
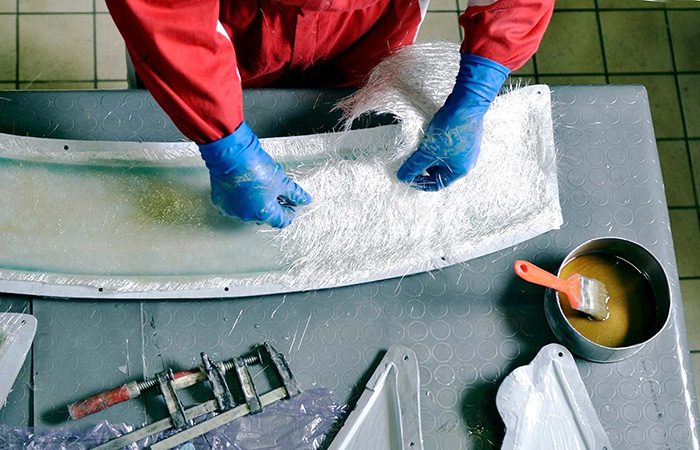
Создание детали из стекловолокна и смолы.
По сути, это было послойное укладывание стеклоткани, пропитанной полимерными смолами, а после затвердевания материала получалась прочная монолитная структура, которая могла выдерживать значительные механические нагрузки. Этот процесс позволял создавать элементы корпуса без сварки и сборки из множества деталей. Роль броневой защиты выполняли керамические элементы. Они вкладывались в специально подготовленные ячейки внутри стеклопластиковых панелей, а после повреждения их можно было бы заменить без полной разборки корпуса. Конечно, были и другие интересные нюансы, например, улучшенная термоизоляция. Впрочем, всё это не меняло того факта, что озвученные мысли плохо соотносились с реальным положением вещей.
Пластик, он везде пластик
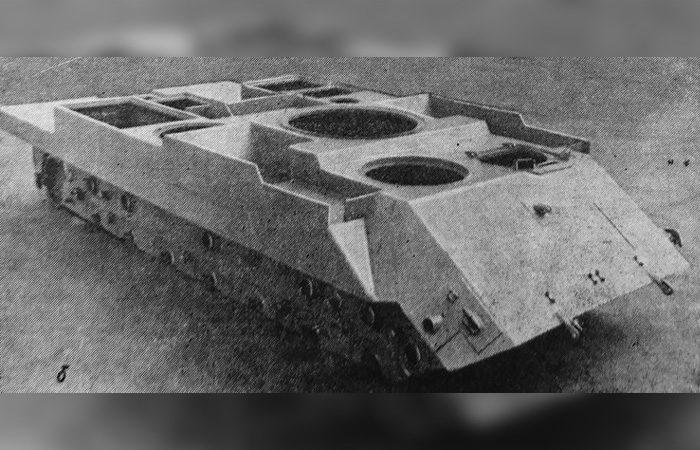
Склеенный из стеклопластика корпус.
Несмотря на очевидные преимущества композитов, у их использования для создания бронетехники имеются большие недостатки. Одна из главных проблем – сильное снижение прочности во время длительной эксплуатации. Стеклопластик, который по своей сути не является монолитным, со временем изнашивается и теряет свои свойства под воздействием ультрафиолета, механических нагрузок и перепадов температур. В боевых условиях, где техника подвергается экстремальным нагрузкам, это наверняка привело бы к быстрому износу корпуса и поломкам. Другой важный момент – сложность ремонта. Если металлическую броню можно было как-то восстановить в полевых условиях, то поврежденные композитные панели ремонту не подлежат вообще, их требуется полностью менять независимо от степени повреждения. То есть оперативный ремонт в полевых условиях превращается в большую и труднорешаемую проблему.
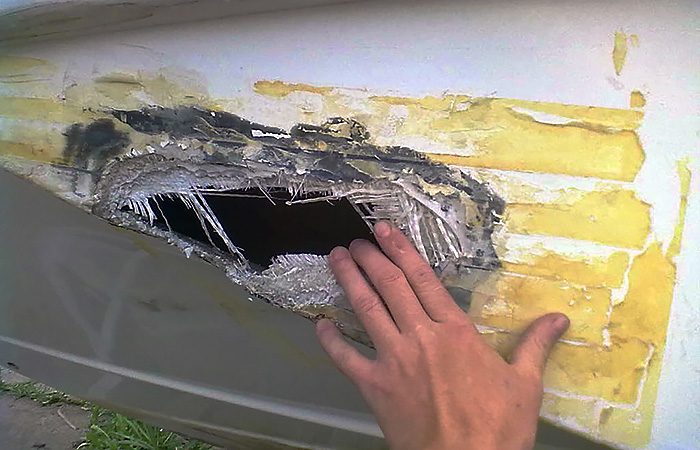
Стеклопластик приходит в негодность от повреждений.
Кроме того, керамические элементы, применяемые для усиления защиты, хоть и обладают высокой твердостью, но остаются хрупкими. При сильных ударах или многократных попаданиях их структура получает большие повреждения, а общая прочность сильно снизится. Конечно, эта проблема довольно быстро решается их полной заменой, но в полевых условиях это наверняка было бы не так просто, как кажется. Не меньше трудностей доставляет химический состав стеклопластика, а точнее, его реакция на высокую температуру. Во время нагрева композит выделяет токсичные вещества, поэтому любой пожар будет нести дополнительную угрозу для экипажа. По этим и многим другим причинам никто всерьёз и не рассматривает создание лёгкой бронетехники из подобных материалов. Уж слишком много сложностей возникает и в процессе производства, и в эксплуатации.
Только зарегистрированные и авторизованные пользователи могут оставлять комментарии.
+1
Немного коряво и не последовательно тут всё изложено. Специфическая тема. Чтобы хорошо это понимать, нужно сильно в неё погрузиться. Неудачная публикация.
- ↓
+1
Вероятно и дальше будут предлагать различные варианты композиционных материалов (смеси, состоящие из двух или более разнородных материалов) и не обязательно использовать углепластик и полимеры. Например, уранокерамические плиты.
- ↓
-3
Конструкторы танков из стеклопластика надеются, что атаковать их будут снаряды из такого же материала.
- ↓
-1
Наука двигатель прогресса!
- ↓
+2
Лучше бы автомобили выпускали, как например в ГДР самым популярным автомобилем с пластиковым кузовом суждено было стать Trabant 601. За 26 лет конвейерной жизни увидели свет 3.1 млн. экземпляров.
- ↓